Introduction
A large clean water service reservoir in the UK serves a population area of around 250,000 homes, providing resilience to any major outage at the nearby water treatment works. The large roof to the reservoir is formed from precast concrete planks with a structural concrete topping. This was previously waterproofed with a sheet applied waterproofing membrane, ballasted to protect from UV degradation. During a maintenance inspection the roof was found to have issues with cracking and due to failures of the existing waterproofing membrane, water ingress.
The challenge
Concrete reservoir roofs are subject to thermal expansion and contraction due to external temperature variations. Where the construction involves pre-cast elements, the thermal movement can lead to an increased risk of cracking. Common high risk locations include plank to plank interfaces and end joints, particularly where rotation can occur over beams.
Where the waterproofing membrane has insufficient resistance to dynamic cracking and flexural fatigue, a failure of waterproofing integrity can result, as occurred here.
The client required a replacement waterproofing system to ensure that the service reservoirs’ flat roof was watertight for the long term. In addition, not only was a solution required to mitigate risks from ongoing movement in the concrete roof, but also to reduce future thermal movement in the roof slab.
The solution
Specialised environments need specialised solutions. Following an engineering assessment by the clients’ appointed engineering consultants, storage asset maintenance framework providers CRL and waterproofing system manufacturer, Triflex worked closely to provide an innovative solution. The result incorporated an inverted insulated build up to reduce the thermal loadings on the large concrete roof.
In many cases existing membranes can be overlaid. Here, to enable a thorough understanding of the issues with the concrete and any concrete repairs to be carried out, the team determined that the ballast and existing failed waterproofing membrane should be fully removed.
On site testing services determine the best solution
The Triflex Technical team conducted a series of on-site tests to determine the most appropriate preparation, priming and waterproofing solution. Triflex systems are highly compatible with the widest range of substrates. In this instance the Triflex Technical team conducted both peel strength and adhesive / cohesive strength tests to determine and validate the final solution.
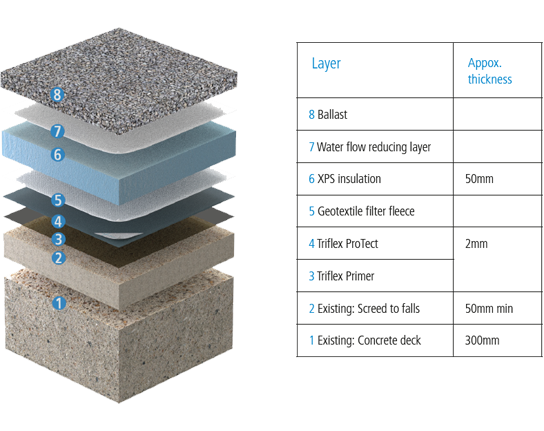
Bespoke Triflex project specification
The bespoke Triflex project specification proposal detailed all processes for the inverted roof waterproofing including:
- Preparation
- Priming
- Surface repairs
- Detail waterproofing: Triflex ProDetail
- Main area waterproofing: Triflex ProTect
Inverted build up comprising:
- Geotextile filter fleece
- 50mm XPS insulation (extruded polystyrene)
- Water flow reducing layer
- Ballast
Dynamic crack bridging for long term confidence
Although the clients’ aim was to reduce thermal movement, the Triflex ProTect fully reinforced liquid applied waterproofing membrane for the main area and the Triflex ProDetail membrane for the details have exceptional crack bridging properties. Both are certified to BS EN 1504-2 and ETAG 005. The BS EN 1504-2 certification includes B4.2 (-20°C) dynamic crack bridging under BS EN 1062-7, the highest classifcation.
The test simulates a crack forming from nothing to 0.5mm and the low temperature makes the test particularly challenging, as all membranes become harder at lower temperatures. Included over the rigorous 9.25 hours of testing are 1,000 larger movements and 20,000 higher frequency smaller movements.
ETAG 005 includes fatigue testing under TR008 Determination of the resistance to fatigue movement. Under this testing the Triflex ProTect and Triflex ProDetail have been tested for their cyclic crack bridging ability from 0mm to 2mm at -10°C for 1,000 cycles.
This certification and testing gave the client the confidence that the solution would have the dynamic crack bridging capability to deal with significant movement in the concrete substrate. In addition, the Triflex ProTect system has a BBA durability statement which states ‘Under normal service conditions, the system will have a service life in excess of 25 years.’ and ETA certification with a working life of 25 years giving the client long term confidence.
Hydrolysis resistance for long term protection
Triflex ProTect is based on polymethyl methacrylate (PMMA) resin technology which is ideal in inverted applications. The resin is resistant to hydrolysis (break down by water), proven in its widespread use in everything from fish tanks to shower trays, baths and worktops. This property means the waterproofing resin will not break down in water, so ponding water poses no threat to its longevity in this shallow 1:200 fall flat roof.
As well as removal of the existing failed membrane and adhesives using a planer, concrete repairs and screed treatments were undertaken by CRL. Following preparation and priming, Triflex PMMA based repair materials were used on the upstands to hatches providing a rapid repair prior to detail waterproofing with Triflex ProDetail. Prior to waterproofing the main area with Triflex ProTect, all cracks were overbanded with a reinforced strip of Triflex ProTect with this double reinforced layer further increasing the crack bridging ability of the system.
All components of the Triflex systems rapidly cure providing rainproof protection in as little as 30 minutes, and fully cure within approximately 60 minutes even in winter temperatures allowing predictable project delivery all year round.
Improved thermal performance and outstanding certified waterproofing
Due to the rapid curing properties of Triflex systems, together with the simple, single process application, the installation of the Triflex waterpoofing system was quickly achieved. For the programme this meant that the inverted roof build-up comprising of geoxtextile filter fleece, with a subsequent 50mm XPS insulation, water flow reducing layer and ballast could be installed without delay.
The inverted build-up was demonstrated by engineers to significantly reduce the indicative calculated thermal variation for the underlying concrete slab. As part of the works a surrounding land drain was installed. Here, the self-terminating Triflex ProDetail system was dressed to the downstand of the slab edge, with the insulation terminating at the leading edge of the slab. The completed ballast-filled land drain then terminated level with the roof’s ballast to fully restrain the insulation.
Project delivery
Triflex components were delivered to site where possible in Intermediate Bulk Containers (IBC’s) to reduce packing waste. With the large expanse, the project delivery was approached by CRL in sections. Whilst the Triflex waterproofing systems are quick and easy to apply to large areas, the geotextile layer and water reducing layer under the ballast are vulnderable to windy conditions making this the most practical this approach for installation.
To ensure the quality of the works, as areas were completed, and prior to installation of the remaining build-up, CRL conducted electronic leak testing of the Triflex ProTect system to ensure watertightness. Trained and supported by Triflex, the highly experienced CRL team consistently deliver Triflex waterproofing across a range of industries to a high standard.